4 de septiembre de 2019
Hace aproximadamente tres años, los técnicos de servicio de KONE en los Países Bajos comenzaron a hacer ruido sobre la cantidad de materiales de desecho que tenían que tratar como parte de sus rutinas diarias. Sus preocupaciones resonaron en la unidad Global Spares Supply (GSS) de KONE, que actúa como una unidad interna centralizada de suministro de repuestos, proporcionando piezas para el negocio de servicios de KONE en todo el mundo.
Se propusieron trabajar con el equipo holandés para estudiar varias soluciones. Uno de ellos fue reemplazar las cajas de cartón de un solo uso que se utilizan convencionalmente en las entregas de repuestos a los técnicos de servicio por cajas de plástico livianas, apilables y reutilizables que permiten reducir o incluso eliminar por completo los materiales de empaque. Además, las cajas reciclables permitieron la adopción de un nuevo proceso centralizado de eliminación de residuos que elimina aún más las emisiones.
Cajas mágicas
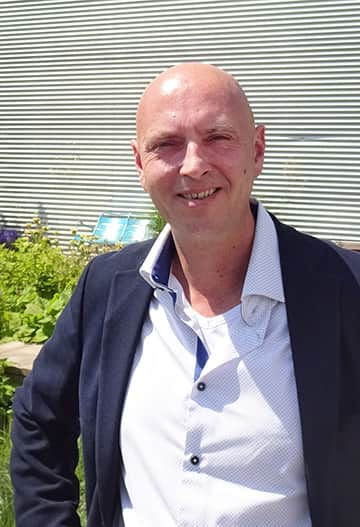
Jacques van Hettema, el gerente de abastecimiento de la unidad en KONE Holanda, está ansioso por resumir las ventajas del piloto que se configuró para probar las cajas de plástico y el nuevo modelo operativo.
“Observamos varios procesos logísticos. Descubrimos que podemos consolidar las entregas semanales y nocturnas de un transportista externo en los Países Bajos a los técnicos. Además, las cajas no requieren el uso de cartón o materiales de relleno de espuma. Además, implementamos un sistema de devolución de residuos utilizando las mismas cajas ”.
Van Hettema señala que el proceso circular es sencillo, por no mencionar eficiente. Así es como funciona: el técnico de servicio llena la caja con cualquier material de embalaje restante y piezas dañadas después de un trabajo. Las cajas se recogen del coche del técnico de servicio y se devuelven al centro de distribución central en Voorschoten, en el oeste de los Países Bajos. Aquí, hay varios contenedores en el sitio para los diferentes tipos de desechos y piezas que se devuelven para su eliminación o reciclaje. Cada caja tiene un código único, que se escanea y se vincula al técnico de servicio, lo que facilita el seguimiento de las cajas y su mantenimiento en circulación.
“El técnico de servicio nunca estará sin la caja y los materiales necesarios para una llamada de servicio”, dice van Hettema. “Dado que el almacén de KONE en Europa central tiene su sede en Alemania, nuestros envíos semanales nocturnos tardan un máximo de siete horas en coche. El técnico de servicio ya no tiene que conducir a varios lugares para desechar los materiales de embalaje o las piezas dañadas, por lo que esto reduce enormemente nuestras emisiones de gases de efecto invernadero ".
Siguientes pasos
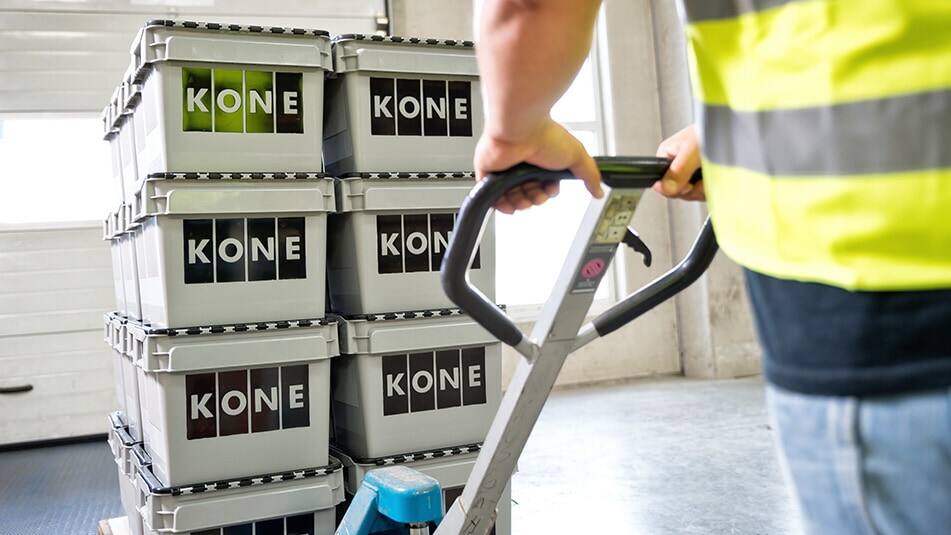
El proyecto piloto holandés se puso en marcha a principios de junio de 2019, casi al mismo tiempo que una gran tormenta azotó los Países Bajos. “No se preocupe, nuestras cajas son impermeables y pueden sujetarse firmemente al asiento trasero del automóvil con un cinturón de seguridad”, se ríe van Hettema. El éxito de la prueba piloto ha llevado a que los 250 técnicos de servicio de elevadores de KONE Países Bajos ahora utilicen las cajas.
“Seguiremos de cerca sus hallazgos y, si todo funciona de acuerdo con el plan, también podemos aplicar este proceso a nuestros técnicos de servicio de escaleras eléctricas”, dice van Hettema.
A nivel mundial, KONE planea llevar este modelo comercial circular al siguiente nivel llevándolo a otros países y expandiéndolo también a otros modos de transporte.
“Este proceso de entrega, combinado con devoluciones a través del mismo flujo y la eliminación centralizada de residuos, nos permite reducir significativamente los residuos de embalaje, el tiempo que nuestros técnicos pasan conduciendo en sus coches y, por tanto, también nuestras emisiones de gases de efecto invernadero”, dice Anselmi Tuominen. .
En su papel como propietario del proceso de gestión de materiales de KONE para el negocio de mantenimiento y las operaciones globales de GSS, Anselmi ha trabajado en estrecha colaboración con el equipo holandés en este piloto y está entusiasmado con la perspectiva de reducir aún más el impacto medioambiental de KONE mediante la expansión del modelo en las primeras fases para otros países de Europa Central.